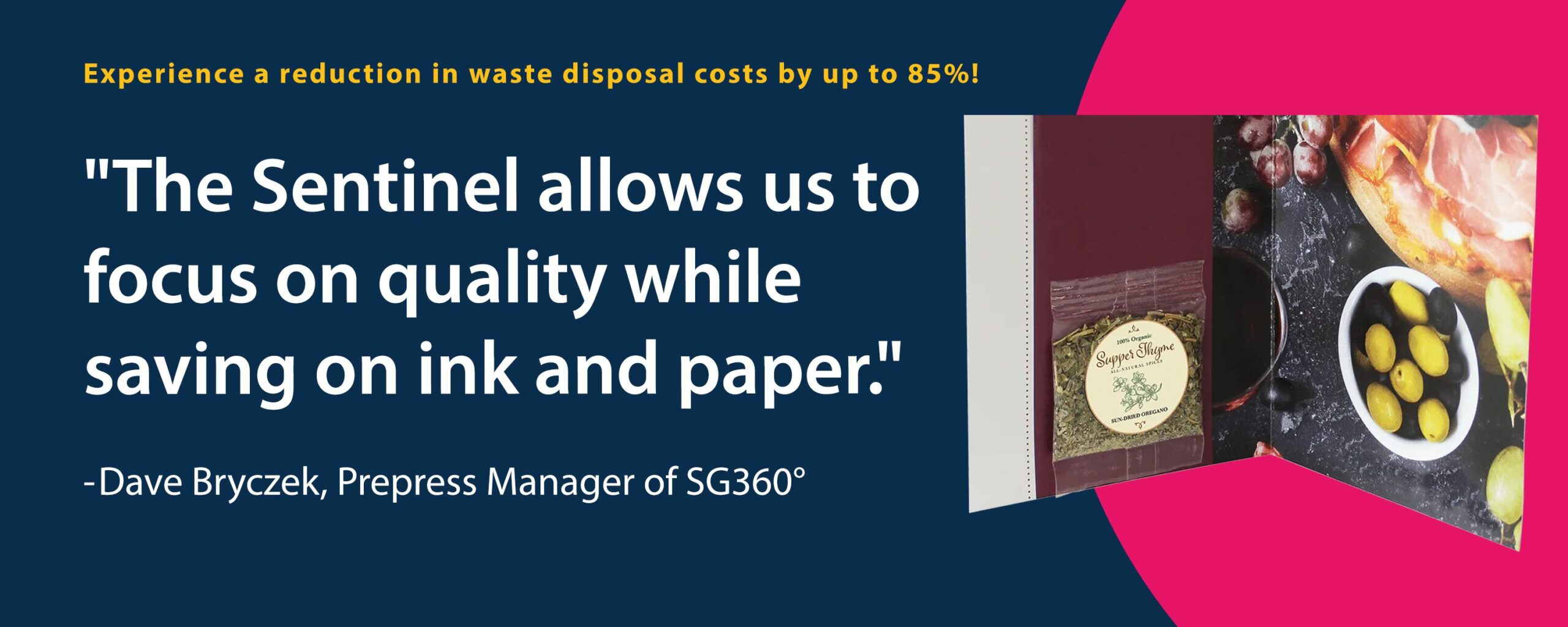
Employing Sentinel automated ink dispensing cartridges on Komori sheetfed-offset presses since 2007, Chicago-area print firm hopes to ‘bolt on’ a fourth system in early ’25.
CARROLLTON, TX – October 28, 2024 – Sentinel, a global leader in automated ink management systems, first delivered a Sentinel iPro to the SG360° Wheeling, IL facility 17 years ago. Then known as Segerdahl Graphics, its first Sentinels came as standard equipment on the 40-inch (B1 format), six-color Komori Lithrone GL Series presses purchased in 2007 and ’09. Ten years later, another Sentinel system came installed on a new eight-color addition to the 80,000 square-foot plant, which employs nearly 100 people running three shifts five days per week (Monday through Friday).
“We produce primarily direct-mail marketing as well as labels at our Gilman Avenue operation in Wheeling,” says Prepress Manager Dave Bryczek, a 36-year printing industry veteran who joined SG360° in 2014. Much of that direct mail work involves special coatings, he adds. Ranked among the top three direct mail producers in the United States, the company bills itself as a marketing agency. Earlier this year, wide-web capabilities, with full inline finishing, were added to its growing digital-print platform.
On the offset side of the house, “maintaining a constant amount of ink in the fountain is one of Sentinel’s major benefits,” notes Bryczek. “The precise ink dispensing of the Sentinel iPro helps with color consistency and frees up press operators for other tasks.” Sentinel iPro’s ultrasonic sensor monitors the amount of ink in the fountain and auto-replaces it where needed. The system reduces: 1) run waste from overfilling, 2) ink spoilage and 3) skinning. “With the Sentinel, it’s much less labor intensive to load the cannisters than to [manually] scoop out ink,” he explains. “Without it, second pressmen and helpers would be troughing out ink almost non-stop.”
4th Sentinel coming next year
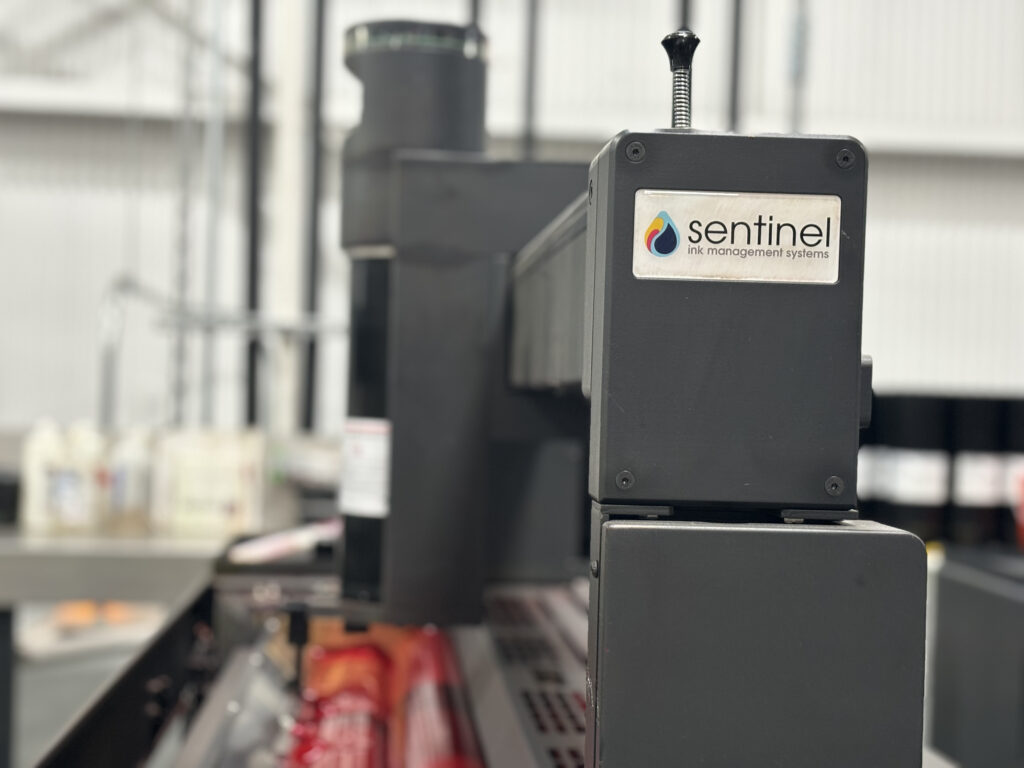
Bryczek and his team like Sentinel iPro so much that they’re planning on adding a fourth iPro system to a Komori Lithrone six-color press early next year. “We track the number of [ink] cannisters used, and we definitely are not wasting as much ink on our presses equipped with Sentinel. Reduced paper waste is another ROI (return on investment) factor. “When running on the Sentinel presses, we get up to color quicker with fewer adjustments made,” he points out.
David Doucette, sales director for Sentinel Ink Management Systems, concludes: “We look forward to working again with SG360° in 2025 and saving them even more money on consumables at their Gilman facility in northern Illinois.” The Sentinel system has reduced waste disposal costs by as much as 85% for several printers.