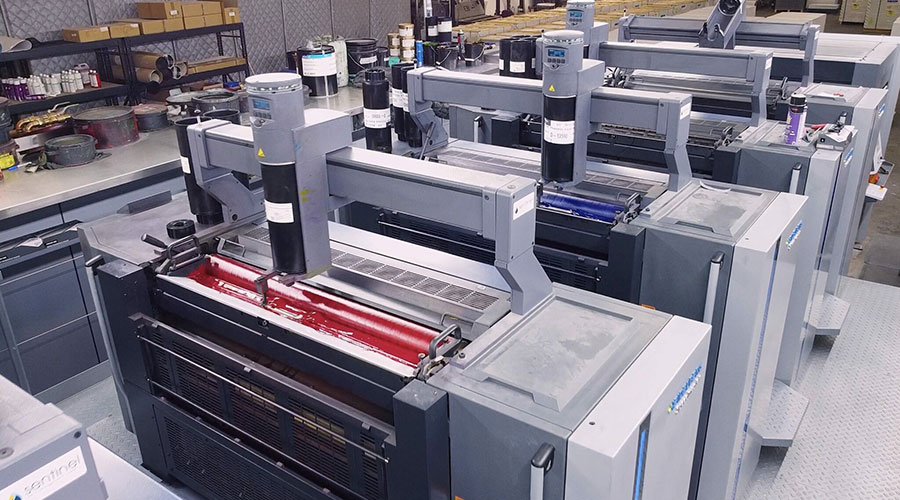
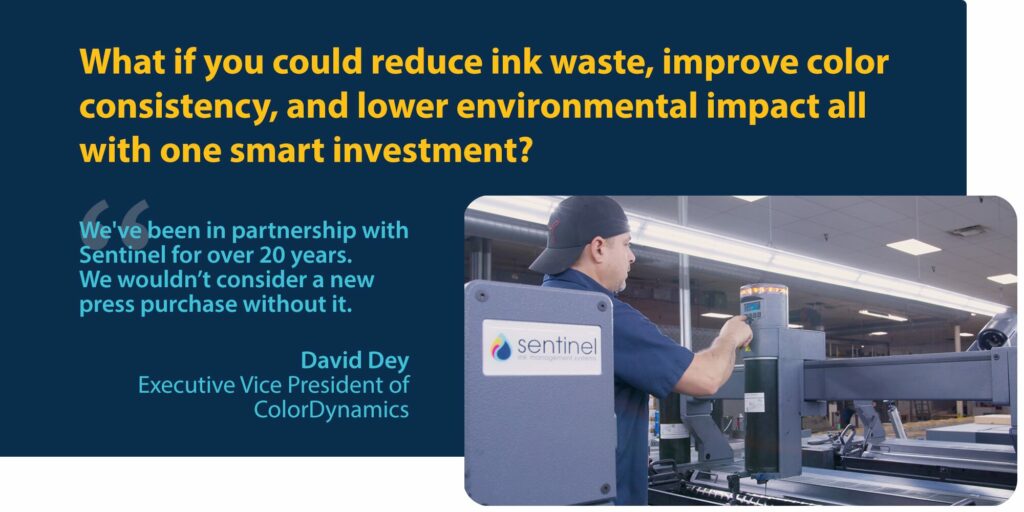
CARROLLTON, TX – January 13, 2025 – Sentinel, a global leader in automated ink management systems, announces the successful installation of another Sentinel iPro ink-management system at ColorDynamics. Based in Allen, TX, ColorDynamics is a leading print service provider that recently upgraded its fleet of sheetfed-offset presses with a new, full-size (40-inch) Speedmaster CX 104 six-color Heidelberg press. This is the seventh installation of the Sentinel iPro automated ink management system on its fleet of sheetfed offset presses since its initial installation in 2004.
For ColorDynamics, the decision to implement Sentinel technology nearly two decades ago marked a turning point in its approach to efficiency and sustainability. Each new printing press purchased by the company is equipped with the Sentinel iPro system, reflecting its vital role in daily production. “Our pressroom manager absolutely loves the Sentinel,” says David Dey, Executive Vice President of ColorDynamics. “I don’t think he’d allow us to buy a piece of equipment without it!”
“The Sentinel iPro frees up my helpers, allowing them to focus more on the feeder end of the press,” explains Dan Collins, Pressroom Manager, and 42-year printing veteran at ColorDynamics. “It maintains constant fountain levels, which significantly improves color consistency, particularly on heavy-coverage jobs.”
Precision and Sustainability in Pantone Printing
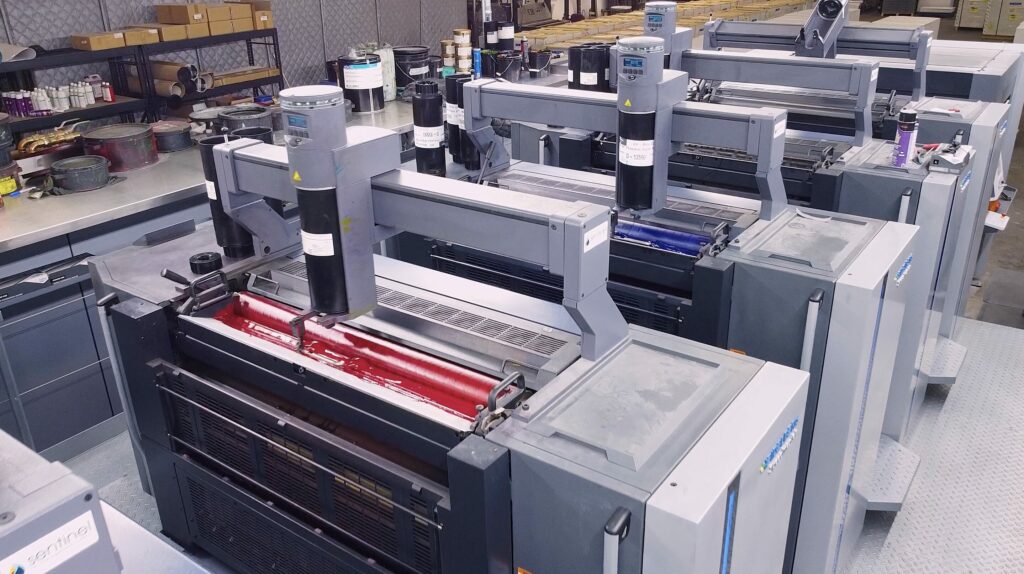
ColorDynamics specializes in custom Pantone ink formulations, a cornerstone of its diverse portfolio, which includes general commercial printing, direct marketing materials, and point-of-purchase displays. The company’s 350,000-square-foot facility also houses digital presses, inline finishing equipment, and extensive mailing and fulfillment capabilities.
“The Sentinel systems are invaluable and vital to our production,” says Dey, who has overseen operations since 2015. With walls of active Pantone Matching System (PMS) cartridges ready for use, the Sentinel system simplifies ink changeovers, reducing manual input and ensuring consistent color quality.
“The changing of ink cannisters and moving from one PMS color to another all happens so quickly and easily,” Dey notes. “The quality and consistency of our printed sheets are better, too, because we are not piling ink into the fountains manually.”
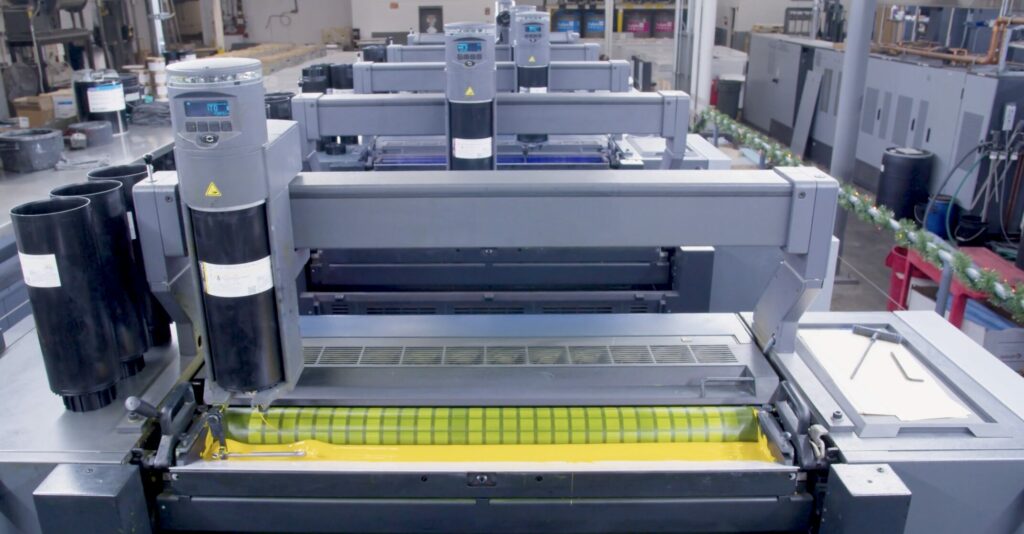
ColorDynamics relies on accurate ink measuring for what it uses per job. From a cost-accounting and return-on-investment (ROI) standpoint, “we have a great understanding of how much ink we use,” he continues. “We track everything — each color on every job – and there’s far less waste left in the fountains thanks to the Sentinels. Less spoilage translates to savings in waste-disposal costs, which add up, according to Dey. Another benefit is a more controlled storage system of ink that has been mixed.
Dey urges fellow printers not to downplay sustainability. “Because the Sentinels keep fountains level, at a certain height, we don’t have an excess of ink put in the fountains to begin with,” he illustrates. “The amount of waste is substantially reduced, which puts less stress on our environment. That’s important to us.”
Adapting Technology for Legacy Presses
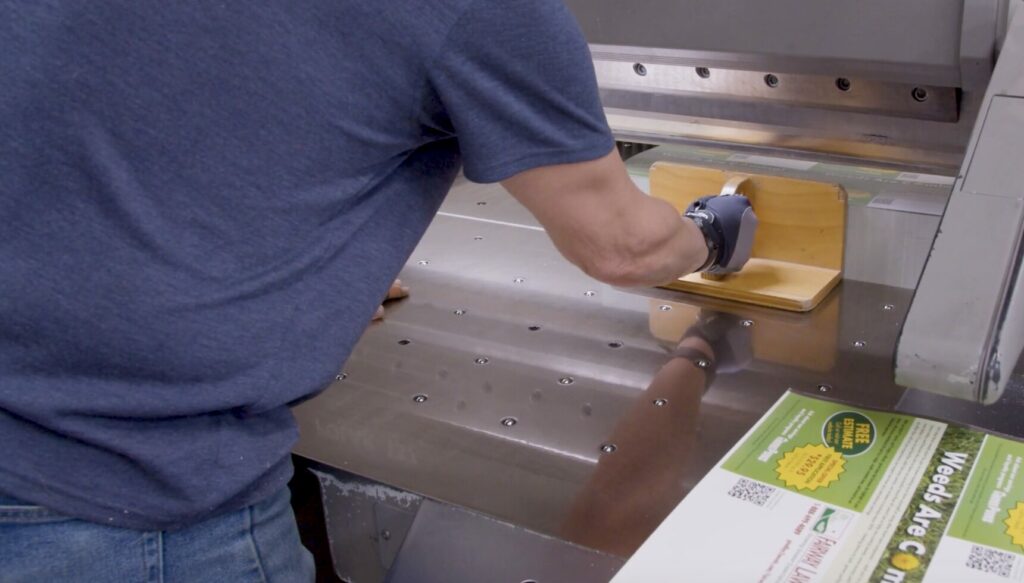
The benefits of Sentinel systems extend beyond new installations. David Doucette, Sales Director for Sentinel Ink Management Systems, highlights its application in retrofitting older presses. “Retrofitting Sentinel onto used machines ensures they operate efficiently and with modern automation capabilities,” Doucette says. “This represents a significant opportunity for printers to extend the life and productivity of their equipment. With its unwavering focus on quality, efficiency, and environmental stewardship, ColorDynamics continues to lead the way in innovative print production, proving that operational excellence and sustainability can go hand in hand.”