Having spent considerable time in the box business, I’ve witnessed firsthand the challenges my clients face. Questions constantly arise: Is the box perfectly square? Are the graphics printed crisply? Is the solid coverage satisfactory? The list of concerns seems endless.
As a producer of anilox rolls, our focus often revolves around print quality, but we mustn’t overlook the significance of the corrugated board itself. After all, it serves as the very foundation upon which we build.
The adhesive or starch utilized to bind the linerboard and corrugating medium together plays a pivotal role in determining the strength and stability of the final product. The entire process of starch application is continually changing on the corrugator. Gel point, viscosity and rheology of the starch changes in the process of application. Heat and constant recirculation breaks starch down so it is imperative that control of the application be as accurate as possible.
Corrugated board in today’s market, is, in many cases, considerably different from board produced years ago. Running much lighter weight liners and mediums in many cases, along with micro flute profiles, requires that starch application be very well controlled and precise.
Too much or uneven application can lead to wet and warped board which slows down the converting process. Washboarding caused by excessive starch application leads to poor graphics quality.
The companies who design, manufacture and service the corrugator of today fully understand that some of the issues in the production of corrugated board that were around years ago, are still with us today, even though, as pointed out above, board grades and flute profiles have changed dramatically.
The application of an optimal starch formula in the corrugated process determines whether the board produced is the best it can be. Many quality issues can all be traced to starch application. That application is controlled by many factors. But without question, one of those factors is the condition of the glue roll set that is charged with applying starch to the flute tips at the single facer and glue machine.
It goes back to basics. Too much or too little, when it comes to starch application, has so much to do with the quality of board coming off the corrugator.
Ensuring the uniform application of starch is imperative, requiring careful attention to the maintenance and replacement of engraved glue and metering rolls as needed.
Consider this as part of your corrugator maintenance procedure. If you are not already doing so, check run out to make sure that the glue roll set is running to OEM specifications.
Similar to the maintenance of anilox rolls, regular audits of the glue roll’s condition should be an integral part of your maintenance regimen. When it’s time to re-engrave the glue roll, seeking expert advice on optimal processes is crucial. For instance, opting for a stainless steel glue roll engraved to specification can eliminate the need for chrome plating and significantly extend roll life. Likewise, on the metering roll, options such as stainless or tungsten carbide surface treatments offer superior longevity compared to traditional chrome.
Commencing with corrugated board produced with uniformity lays the groundwork for the creation of strong boxes that meet or exceed graphic demands, ensuring high levels of customer satisfaction.
In essence, achieving excellence in corrugated box production requires meticulous attention to detail at every stage of the process. From selecting high-quality materials to maintaining precision equipment, every aspect contributes to the overall quality and performance of the final product. By prioritizing the integrity of the corrugated board and implementing best practices in adhesive application, manufacturers can elevate their standards and deliver superior packaging solutions that exceed customer expectations.
25 Quad at 65 BCM, direct engraved into Stainless steel
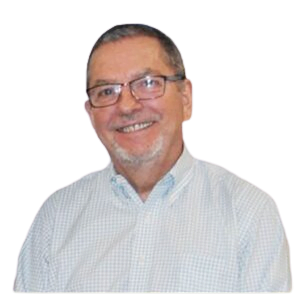
“Check run out to make sure that the glue & metering roll set is running to OEM specifications!”
Frank Greene
Greene House Group